How to Choose the Best CNC Machine Coolant Filtration System
- Gu Zhouying
- 3 days ago
- 5 min read
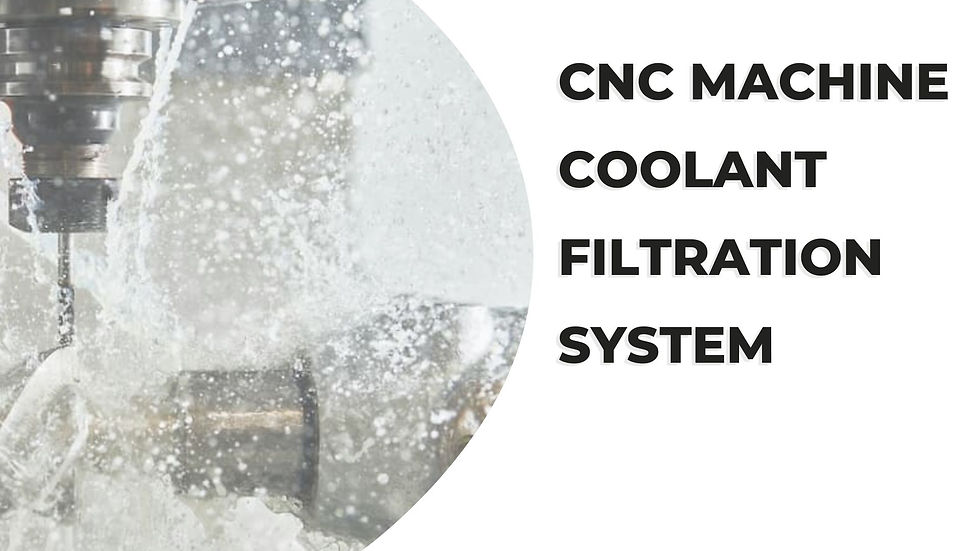
Article Contents:
Introduction
Choosing the right coolant filtration system for your CNC machine might sound like just another checkbox in your setup list—but it’s way more important than that. Think of your coolant as the blood of your machine. If it’s dirty or clogged, the entire system underperforms or even breaks down. That’s where a solid coolant filtration system comes in.
Let’s break this all down so you can make the best decision without getting overwhelmed by technical jargon.
Understanding CNC Coolants
What CNC Coolants Do
CNC coolant or cutting fluid is an industrial fluid commonly used in metal cutting operations for improved efficiency. CNC machining coolant comprises special chemical additives formulated through scientific compound concentration. Its primary elements include animal fat, water, petroleum distillate, vegetable oil, and other raw materials.
These coolants improve the CNC machines’ capability to cut materials such as high-density plastics, fiberglass, and metals while reducing high-temperature build-up.
Types of CNC Coolants
Soluble Oils
Soluble oils, also known as emulsions or water-soluble oils, are excellent coolant choices for general machining purposes and are commonly used amongst water-soluble cutting fluids. Water-soluble oils often create emulsions when mixed with water. The result of the mixture comprises the base mineral oil and the emulsion to create metalworking fluid. It performs well in diluted form and offers excellent lubricity and heat transfer performance.
Soluble oils are cheap and commonly used in the metalworking industry. They comprise 60-90% petroleum, emulsifiers, or mineral oil and adhere to the workpiece during machining. It is ideal for lubrication and offers excellent rust resistance when mixed with a specific amount of rust inhibitor.
Synthetic Fluids
These coolants are the cleanest because they do not contain petroleum or mineral oil. Synthetic fluids comprise rust inhibitors and chemical lubricants that break down in water. These fluids are mixed with water to produce a metalworking fluid. Therefore, these CNC coolants possess high cooling capacity, corrosion prevention, easy maintenance, and lubricity.
Moreover, synthetic fluids are primarily employed in high-heat, high-velocity machining processes like surface grinding because of their excellent cooling capacity. Heavy-duty synthetic fluids are ideal for handling several machining operations.
Synthetics are categorized as simple and complex or emulsifiable synthetics depending on their composition. Simple synthetics or true solutions are commonly used for light-duty grinding. On the other hand, complex synthetic concentrates contain synthetic fluids suitable for moderate to heavy-duty machining procedures. More importantly, complex synthetic lubricants allow high speeds and feed in machining operations.
Semi-Synthetic Fluids
Semi-synthetics are a hybrid of synthetics (polymer) and soluble oils. These fluids contain about 2-30% of mineral or petroleum oil in a water-dilatable concentration. The remaining percentage of a semi-synthetic fluid consists of water and emulsifiers. Other elements in the concentrate include biocide additives, wetting agents, and corrosion inhibitors. They are commonly referred to as performed chemical emulsions because water is its primary ingredient and emulsifies with water during the concentrate’s production.
These semi-synthetic fluids are usually translucent. However, their properties can vary from slightly translucent to opaque. Additionally, many of these semi-synthetics have good heat sensitivity. Hence, semi-synthetic oil molecules surround the cutting tool, ensuring better lubricity.
The Role of Coolant Filtration Systems
How Filtration Impacts Machine Performance
A proper filtration system keeps contaminants like metal shavings, dirt, and bacteria out of your coolant. Cleaner coolant means smoother machining, longer tool life, and fewer maintenance calls.
Benefits of Effective Coolant Filtration
Improved surface finish
Longer coolant life
Reduced machine downtime
Healthier work environment
Key Factors to Consider Before Buying
Type of Contaminants
Are you dealing mostly with metal chips, fine particles, or oils? The type of debris will determine the filtration technology you need.
Volume of Coolant Used
Bigger systems need higher-capacity filters. If you’re running multiple machines, you may need a central system.
Type of CNC Machine
Different machines (lathes, mills, grinders) have different requirements. Match the system to your machine’s design.
Maintenance Requirements
Some filters need frequent cleaning. Others are low-touch. Decide how hands-on you’re willing to be.
Budget Constraints
You don’t have to go bankrupt for a good system but don't go too cheap either. It's about balance—get the best value, not just the lowest price.
Types of CNC Coolant Filtration Systems
Gravity Filtration Systems
Basic and budget-friendly. These use gravity to let heavier particles settle at the bottom.
Magnetic Filtration Systems
Perfect for machines that generate ferrous debris. Magnets pull out metal bits from the coolant flow.
Centrifugal Filtration Systems
These systems use spinning force to separate the junk—great for fine particles.
Bag and Cartridge Filters
Simple but effective. Ideal for light to moderate filtering. Just remember to change the filters regularly.
Hydrocyclone Systems
These use fluid velocity to separate solids. No moving parts, low maintenance, and great for high-speed applications.
Advanced Features to Look For
Automated Cleaning
Reduces manual maintenance and downtime.
Sensor Integration
Smart systems monitor coolant cleanliness and let you know when it’s time to clean or replace filters.
Compatibility with Various Coolants
Make sure your system works with all types of coolants in case you switch up later.
Installation and Maintenance Tips
Initial Setup Best Practices
Install near the sump for efficient flow
Check compatibility with your machine’s plumbing
Test flow rate and pressure settings
Routine Maintenance Steps
Clean filters regularly
Monitor coolant condition weekly
Replace filter media as needed
Troubleshooting Common Issues
Clogged filters? Flush or replace them.
Low flow rate? Check for blockages or pump issues.
Weird smells? Might be bacteria—time to clean the tank.
Environmental and Cost Benefits
Reducing Waste and Environmental Impact
Filtered coolant lasts longer, which means you dispose of less. Plus, fewer spills and toxic cleanups—a win-win.
Long-Term Cost Savings
Sure, the system costs upfront. But longer tool life, fewer breakdowns, and extended coolant life save you serious cash in the long run.
Mistakes to Avoid
Overlooking Filtration Capacity
Don’t underestimate your system's needs. Undersized filters get clogged fast and fail when you need them most.
Ignoring Compatibility with Existing Setup
Make sure the system works with your coolant type, tank size, and machine model.
Skipping Maintenance
A neglected filter is useless. If you’re not maintaining it, you’re throwing money away.
Conclusion
Choosing the best CNC machine coolant filtration system doesn’t have to be rocket science—but it does require a bit of thought. Consider your machine, your coolant, and the kind of debris you’re battling daily. Think long-term savings, not just the up-front price. And once it’s installed, don’t forget to maintain it. Your machine—and your wallet—will thank you.
FAQs
1. How often should I replace my coolant filter?
Typically, every 3-6 months, but it depends on your usage and the type of filter system.
2. Can I use the same filtration system for all CNC machines?
Not always. Match the filter to each machine's specific needs for best results.
3. Are magnetic filters enough on their own?
Not usually. They work well for metal particles but won’t catch non-magnetic debris.
4. Is a more expensive filter system always better?
Not necessarily. Focus on the right features, capacity, and compatibility rather than just price.
5. Do filtration systems reduce the smell of coolant?
Yes! Cleaner coolant smells better and lasts longer, reducing that funky shop odor.
For the right treatment system, you need the right expertise.
For more information about our zero liquid discharge systems kindly get in touch at:
🌐 www.yasa.ltd(EN)
🌐 www.yashahuanjing.cn (中文)
📱 +86 136 3643 1077
YASA ET official online store > click here
Comments