Inorganic Polymer Flocculants? All you need to know about PAC
- YASA ET
- 10 gen 2022
- Tempo di lettura: 8 min
Flocculants may not be unfamiliar to professionals who have been working with water
treatment, but which flocculants are there, and how to distinguish and use them correctly seems a very confusing topic among many people.
With the help of this article, YASA ET provide a comprehensive review and explanation of organic flocculants such as Poly-aluminium Chloride (PAC). Let's take a look at it together.
Flocculant is a type of substance that can reduce or eliminate the precipitation stability and polymerization stability of dispersed particles in water, and make dispersed particles coagulate and flocculate into aggregates.
According to chemical composition, flocculants can be divided into three categories:
Inorganic
Organic
Microbial
This article mainly introduces our most commonly used inorganic flocculants for wastewater treatment which include aluminium salts, iron salts and their polymers.
The working principle of flocculants
The colloidal particles in the water have the characteristics of tininess, surface hydration and charging, which makes them have strong stability. When the flocculant is added to the water, it will be hydrolysed into a charged colloid and the surrounding ions to form an electric double layer structure.
The method of rapid stirring after pouring is adopted to promote the collision chance and frequency of the colloidal impurity particles in the water and the micelles hydrolysed by the flocculant. The impurity particles in the water first lose their stability under the action of the flocculant, and then agglomerate into larger particles, and finally settle down or float upwards.
The impurity particles in the water interact with the flocculant to lose or reduce the stability through mechanisms such as the compression of the electric double layer and the electric neutralization, and the process of generating micro flocs is called coagulation. The process of agglomerating to form micro-flocs under the agitation of bridging materials and water flow, through adsorption bridging and sediment net catching and other mechanisms to grow into large flocs is called flocculation.
The combination of mixing, coagulation and flocculation is called coagulation. The mixing process is generally completed in the mixing tank, and the coagulation and flocculation are carried out in the reaction tank.
1. Inorganic Polymer Flocculant
In recent years, inorganic polymer flocculants have been developed into a new type of water treatment reagents, which are more efficient than traditional inorganic flocculants and much cheaper than organic polymer flocculants.
Inorganic polymer flocculants of aluminium, iron and silicon are actually the intermediate products of their processes from hydrolysis, sol to precipitation, namely Al(Ⅲ), Fe(Ⅲ), Si(Ⅳ) hydroxyl and oxygen polymers. Aluminium and iron are positively charged cationic, and silicon is negatively charged anionic. The molecular weight of their units in the water-soluble state is about hundreds to thousands, and they can be combined with each other to form an aggregate with a fractal structure.
Their coagulation-flocculation process is a comprehensive manifestation of the two functions of electric neutralization and adhesion bridging of particles in the water. The particle size of suspended particles in water ranges from nanometres to micrometres, and most of them are negatively charged. Therefore, the positive and negative charge, electrical strength, molecular weight, and aggregate particle size of the flocculant and its form are the main factors that determine its flocculation effect. At present, there are dozens of types of inorganic polymer flocculants, and the output has reached 30% to 60% of the total output of flocculants. Among them, the most commonly used and widely used is poly-aluminium chloride, or PAC.
Al(Ⅲ) and Fe(Ⅲ) hydroxyl and oxygen-based polymers will be further combined into aggregates, which are kept in an aqueous solution under certain conditions, and their particle size is roughly in the nanometre range, so as to exert the cohesion-flocculation effect, it will be low. The result of high dosage.
The advantages of inorganic polymer flocculants are reflected in a better performance and lower costs than traditional flocculants such as aluminium sulphate and ferric chloride.
Poly-aluminium Chloride (PAC)
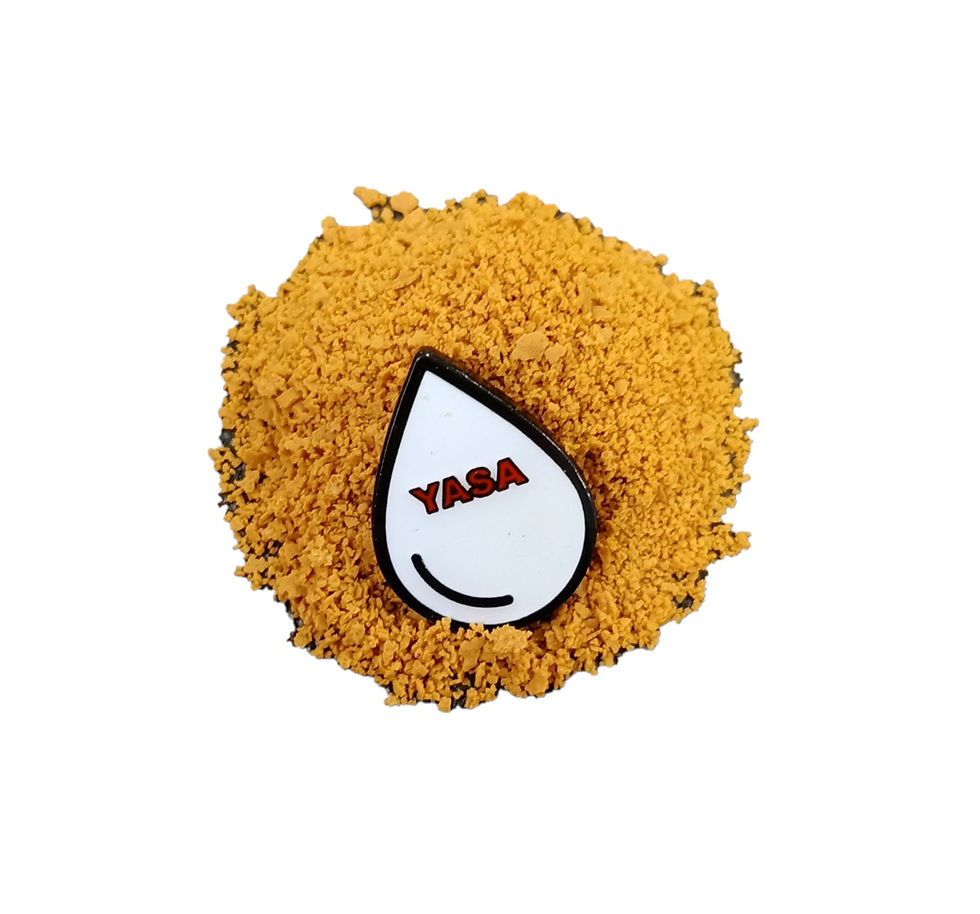
Poly-aluminum chloride, PAC for short, has a chemical formula of ALn(OH)mCL3n-m. PAC is a multivalent electrolyte that can significantly reduce the colloidal charge of clay impurities (multiple negatively charged) in water. Due to the large relative molecular mass and strong adsorption capacity, the flocs formed are larger, and the flocculation and sedimentation performance is better than other flocculants.
PAC has been successfully applied in various treatment processes of water supply, industrial wastewater and urban sewage, including pre-treatment, intermediate treatment and advanced treatment, and has gradually become the mainstream flocculant. However, in terms of form, degree of polymerization and the corresponding coagulation-flocculation effect, inorganic polymer flocculants are still in the position between traditional metal salt flocculants and organic polymer flocculants.
PAC has a high degree of polymerization, and rapid stirring after addition can greatly shorten the formation time of flocs. PAC is less affected by the water temperature, and the effect is also very good when the water temperature is low. It reduces the pH value of water less, and has a wide applicable pH range (it can be used in the range of pH=5-9), so it is not necessary to add an alkali agent. The dosage of PAC is small, the mud output is also small, and it is more convenient to use, manage, and operate, and it is less corrosive to equipment, pipelines, etc. Therefore, PAC has a tendency to gradually replace aluminium sulphate in the field of water treatment. Its disadvantage is that the price is higher than that of traditional flocculants.
In addition, from the perspective of solution chemistry, PAC is the kinetic intermediate product of the aluminium salt hydrolysis-polymerization-precipitation reaction process, which is thermodynamically unstable. Adding certain inorganic salts (such as CaCl2, MnCl2, etc.) or macromolecules (such as polyvinyl alcohol, polyacrylamide, etc.) can improve the stability of PAC, and at the same time can increase the cohesive capacity.
In terms of the production process, one or several different anions (such as SO42-, PO43-, etc.) are introduced in the manufacturing process of PAC, and the polymer structure and morphological distribution can be changed to a certain extent by the use of polymerization, thereby improving The stability and efficacy of PAC; if other cationic components, such as Fe3+, are introduced in the manufacturing process of PAC to make Al3+ and Fe3+ alternately hydrolysed and polymerized, a composite flocculant poly-aluminium iron can be prepared.
2. Factors influencing the effectiveness of flocculants
pH
The pH value of the water has a great influence on the use effect of the inorganic flocculant. The pH value is related to the type of flocculant selected, the dosage and the coagulation sedimentation effect. The H+ and OH- in the water participate in the hydrolysis reaction of the flocculant. Therefore, the pH value strongly affects the hydrolysis rate of the flocculant, the existence form and performance of the hydrolysate.
Take the aluminium salt that achieves coagulation by generating Al(OH)3 charged colloids as an example. When the pH value is less than 4, Al3+ cannot be hydrolysed into Al(OH)3 in a large amount, mainly in the form of Al3+ ions, and the coagulation effect is extremely Difference. When the pH value is between 6.5 and 7.5, Al3+ is hydrolysed and polymerized into Al(OH)3 neutral colloid with a high degree of polymerization, and the coagulation effect is better. After pH value ﹥8, Al3+ is hydrolysed into AlO2-, and the coagulation effect becomes very poor.
The alkalinity of water has a buffering effect on the pH value. When the alkalinity is not enough, lime and other agents should be added to supplement it. When the pH of the water is high, you need to add acid to adjust the pH to neutral. In contrast, polymer flocculants are less affected by pH.
Water Temperature
Water temperature affects the rate of hydrolysis of the flocculant and the rate and structure of alum formation. The hydrolysis of coagulation is mostly an endothermic reaction. When the water temperature is low, the hydrolysis rate is slow and incomplete.
At low temperature, the viscosity of water is large, the Brownian motion is weakened, the number of collisions between the flocculant colloidal particles and the impurity particles in the water is reduced, and the shear force of the water increases, which hinders the mutual adhesion of the coagulated flocs; therefore, despite the increase With the dosage of flocculant, the formation of flocs is still very slow, and the structure is loose and the particles are small, making it difficult to remove.
Low temperature has little effect on polymer flocculants. However, it should be noted that when using organic polymer flocculants, the water temperature should not be too high. High temperature will easily cause the organic polymer flocculants to age or even decompose to produce insoluble substances, thereby reducing the coagulation effect.
Impurities
The uneven particle size of impurities in the water is beneficial to coagulation, and small and uniform particles will lead to poor coagulation effects. Too low concentration of impurity particles is often detrimental to coagulation. At this time, refluxing sediment or adding coagulant can improve the coagulation effect. When the impurity particles in the water contain a large amount of organic matter, the coagulation effect will be worse, and it is necessary to increase the dosage or add oxidants and other agents that play a role in coagulation. Calcium and magnesium ions, sulfides, and phosphides in water are generally beneficial to coagulation, while certain anions and surface active substances have an adverse effect on coagulation.
Types of flocculants
The choice of flocculant mainly depends on the nature and concentration of colloids and suspended solids in water. If the pollutants in the water are mainly in a colloidal state, inorganic flocculants should be the first choice to make them destabilize and agglomerate. If the flocs are small, it is necessary to add a polymer flocculant or use a coagulant aid such as activated silica gel.
In many cases, the combined use of inorganic flocculants and polymer flocculants can significantly improve the coagulation effect and expand the scope of application. For macromolecules, the greater the amount of charge on the chain molecules, the higher the charge density, the more fully extended the chain, the greater the range of adsorption and bridging, and the better the coagulation effect.
Flocculant Dosage
When coagulation is used to treat any wastewater, there is an optimal flocculant and an optimal dosage, which are usually determined by experiments. Excessive dosage may cause the stability of the colloid. Generally, the dosage range of ordinary iron salt and aluminium salt is 10-100mg/L, the dosage of polymer salt is 1/2~1/3 of the dosage of ordinary salt, and the dosage range of organic polymer flocculant is 1~5mg/L. .
Dosing sequence of flocculant
When using multiple flocculants, it is necessary to determine the best dosing order through experiments. Generally speaking, when the inorganic flocculant is used together with the organic flocculant, the inorganic flocculant should be added first, and then the organic flocculant should be added.
When the particle size of the treated impurities is above 50μm, the organic flocculant is often added to absorb the bridge first, and then the inorganic flocculant is added to compress the electric double layer to destabilize the colloid.
Hydraulic Conditions
In the mixing stage, the flocculant and water are required to mix quickly and evenly. In the reaction stage, it is necessary to create enough collision opportunities and good adsorption conditions to allow sufficient growth opportunities for the flocs, and to prevent the small flocs that have been formed from being Broken, so the stirring intensity should be gradually reduced, and the reaction time should be long enough.
Contact Us
YASA ET cooperate with many companies in different industries, including ZF, Schaeffler, ABNEN and many others for their wastewater treatment projects.
Our customers cover multiple industries and fields such as auto parts manufacturing, surface treatment, semiconductors, bearings, metal works, just to name a few.
For more information about our technology and services, kindly get in touch with our team:
📧 info@yasa.ltd
🌐 www.yasa.ltd
📱 +86 136 3643 1077
Visit YASA ET official online store, click here
Comentarios