Electrocoagulation (EC) VS Electro-oxidation (EO)
- YASA ET
- ٢٦ أغسطس ٢٠٢٢
- 6 دقائق قراءة
In this article we present and analyse the main features of Electrocoagulation (EC) and Electro-oxidation (EO) wastewater treatment technologies.
If you want to learn more about these treatment systems, technologies and applications, continue reading this article.
What is Electrocoagulation (EC)?
An Electrocoagulation (EC) system essentially consists of pairs of conductive metal plates in parallel, which act as monopolar electrodes suspended in an electrolytic cell containing wastewater. Direct current is passed through the electrodes (anode and cathode) to start the electrochemical treatment.
The conductive metal plates are commonly known as "sacrificial electrodes." The sacrificial anode lowers the dissolution potential of the anode and minimizes the passivation of the cathode. The sacrificial anodes and cathodes can be of the same or of different materials.
During the process of electrocoagulation, the following reactions occur at the electrodes:
· The anode is oxidized to ferrous or aluminium ions (depending on the material chosen)
· At cathode, water molecules are lysed to protons (H+) and hydroxyl ions (OH–)
Electrocoagulation (EC) Working Principle
Electrocoagulation consists of pairs of metal sheets called electrodes, that are arranged in pairs of two—anodes and cathodes. Using the principles of electrochemistry, the cathode is oxidized (loses electrons), while the water is reduced (gains electrons), thereby making the wastewater better treated.
Electrocoagulation process effects cause the removal, reduction and oxidative decomposition of pollutants and separates them from the water body. The sludge settles at the bottom of the electrocoagulation reactor, while the flocs float at the top.

What is Electro-oxidation (EO)?
Electro-oxidation (EO), also known as anodic oxidation or electrochemical oxidation, is a technique used for wastewater treatment, mainly for industrial effluents, and is a type of advanced oxidation process (AOP). The most general layout comprises two electrodes, operating as anode and cathode, connected to a power source.
Electrooxidation (EO) Working Principle
Electrooxidation (EO) or Electro-oxidation (EO) process involves the application of an external source of energy into an electrochemical cell that contains one or more pairs of electrodes. At the cathode, a reduction reaction occurs, and the oxidation reaction takes place at the anode.
When an energy input and sufficient supporting electrolyte are provided to the system, strong oxidizing species are formed, which interact with the contaminants and degrade them. The refractory compounds are thus converted into reaction intermediates and, ultimately, into water and CO2 by complete mineralization.
Electrooxidation (EO) can eliminate contaminants at the interface of the anode/aqueous solution (direct oxidation), and via anodically generated intermediates e.g. reactive oxygen species like hydroxyl radicals (HO•) and active chlorine species (indirect oxidation).
Hydroxyl radicals are highly reactive oxidants that can react with nearly all organic contaminants and eventually mineralize them to CO2 and H2O non-selectively in ambient pressure and atmospheric temperature.
Electrocoagulation (EC) and Electro-oxidation (EO) Pollutants Removal
Both Electrocoagulation (EC) and Electro-oxidation (EO) are very effective in removing certain pollutants from water. Both technologies can significantly reduce the levels of COD, BOD and TDS, Nitrates and Ammonia in wastewaters.
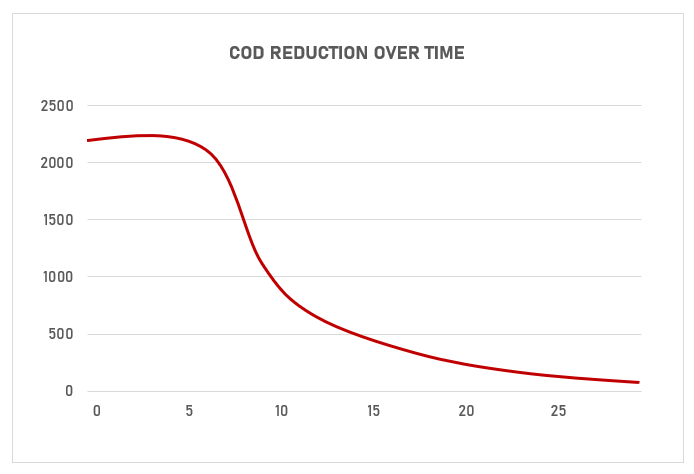
A more accurate assessment of these technologies treatment capacities can be made by using YASA ET test equipment designed for EC and EO.
Electrocoagulation and Electrooxidation Electrodes Material
Electrocoagulation and Electrooxidation electrodes material need to be carefully selected mostly by analysing the pollutants that we want to remove or reduce from the wastewater.
Carbon and Graphite Electrodes
Electrodes based on carbon or graphite are common due to their low cost and high surface area. Also, they are able to promote adsorption of contaminants on their surface while at the same generating the radicals for electro-oxidation. However, they are not suited for working at high potentials, as at such conditions they experience surface corrosion, resulting in reduced efficiency and progressive degradation of the exposed area. In fact, the overpotential for oxygen evolution is quite low for graphite.
Platinum Electrodes
Platinum electrodes provide good conductivity and they are inert and stable at high potentials. At the same time, the oxygen evolution overpotential is low and comparable to that of graphite. As a result, electro-oxidation with Platinum electrodes usually provides low yield due to partial oxidation of the compounds. The contaminants are converted into stable intermediates, difficult to be broken down, thus reducing current efficiency for complete mineralization.
Mixed Metal Oxides (MMOs) Electrodes
Mixed Metal Oxides (MMOs), also called Dimensionally Stable Anodes (DSA), are devices with high conductivity and corrosion resistance for use as anodes in electrolysis.
The kind of electrodes are very popular in electrochemical process industry, because they are very effective in promoting both chlorine and oxygen evolution. In the case of wastewater treatment, they provide low current efficiency, because they favour the competitive reaction of oxygen evolution. Similarly to Platinum electrodes, formation of stable intermediates is favoured over complete mineralization of the contaminants, resulting in reduced removal efficiency.
Due to their ability to promote chlorine evolution reaction, dimensionally stable anodes are the most common choice for processes relying on mediated oxidation mechanism, especially in the case of chlorine and hypochlorite production.
Lead Dioxide Electrodes
Lead dioxide electrodes have long been exploited in industrial applications, as they show high stability, large surface area, good conductivity and they are quite cheap. In addition, lead dioxide has a very high oxygen evolution overpotential, which implies a high current efficiency for complete mineralization. Also, lead dioxide electrodes were found to be able to generate ozone, another strong oxidizer, at high potentials.
Boron-doped Diamond (BDD) Electrodes

Synthetic diamond is doped with Boron to raise its conductivity, making it feasible as electrochemical electrode. Once doped, BDD electrodes show high chemical and electrochemical stability, good conductivity, great resistance to corrosion even in harsh environment and a remarkable wide potential window.
For this reason, BDD is generally considered as the most effective electrode for complete mineralization of organics, providing high current efficiency as well as lower energy consumption compared to all other electrodes. At the same time, the manufacturing processes for this electrode, usually based on high temperature CVD technologies, are very costly.
Electrocoagulation and Electrooxidation Wastewater Treatment Applications
Both Electrocoagulation and Electrooxidation have been applied to treat a wide variety of wastewaters.
Electrocoagulation can be used for treating many kinds of wastewaters, including emulsions, metalworking fluids, washing and rinsing, laundry effluents, etc. Some examples can be found here.
Electrooxidation was proven effective for the removal and treatment of wastewaters with harmful and non-biodegradable contaminants, including aromatics, pesticides, drugs and dyes. It can also be effective in the removal of nitrates and ammonia with custom electrodes, such as BDD.
Electrocoagulation and Electrooxidation can also be combined to remove pollutants and reach optimal treatment results. The first treatment stage is usually made by Electrocoagulation (EC), while the second stage by Electrooxidation (EO).
Electro-oxidation (EO) Costs
Electro-oxidation (EO) has relatively high operating costs, it is often combined with other technologies. Electro-oxidation can be paired with other electrochemical technologies such as electrocoagulation, consecutively or simultaneously, to further reduce operational costs while achieving high degradation standards.
Electrooxidation has recently grown in popularity thanks to its ease of set-up and effectiveness in treating harmful and recalcitrant organic pollutants, which are typically difficult to degrade with conventional wastewater remediation processes. Also, it does not require any external addition of chemicals (contrarily to other processes like in-situ chemical oxidation), as the required reactive species are generated at the anode surface.
Electrocoagulation (EC) Costs
Electrocoagulation (EC) has relatively low operating costs compared to Electro-oxidation (EO) and other technologies.
In fact, the main cost of Electrocoagulation (EC) is the electrodes that need to be replaced every 4-5 months, depending on the wastewater to be treated. Since the electrodes are usually Iron or Aluminium plates or rods the manufacturing process is simple and the majority of the costs are in the raw materials.
Furthermore, an additional cost can be from chemicals used to enhance the reaction effect and treatment results of Electrocoagulation, so the operational expenses could slightly increase based on the quantity used. For an estimations of costs you can get in touch with our team by clicking here.
Should I Use Electrocoagulation (EC) or Electrooxidation (EO) for the Treatment of my Wastewater?
Electrocoagulation (EC) and Electrooxidation (EO) are frequently used as part of treatment systems for industrial wastewaters. Depending on the pollutants that need to be removed Electrocoagulation can be combined with Electrooxidation.
Normally the correct equipment configuration and electrodes material can make a difference in the treatment performance, so they need to be selected and carefully manufactured to reach the optimal results.
The first step before choosing Electrocoagulation or Electrooxidation for a wastewater treatment system is to analyse the chemical composition and pollutants contained in the industrial effluent to be purified. Secondly, extensive testing needs to be undertaken to find the correct electrodes and flow parameters for treating the specific wastewater. Finally, the right EC or EO equipment for the treatment system can be manufactured and can be installed at the client site.
For the correct functioning of Electrocoagulation and Electro-oxidation treatment systems, you need the right expertise. For more information about our wastewater treatment systems kindly get in touch at:
🌐 www.yasa.ltd(EN)
🌐 www.yashahuanjing.cn (中文)
📱 +86 136 3643 1077
YASA ET official online store > click here
Sources:
Comments